カーエレクトロニクス、航空/宇宙向けなどの高信頼性プリント配線板
高発熱IC向けプリント配線板の耐熱信頼性評価に最適!
信頼性評価の課題を解決
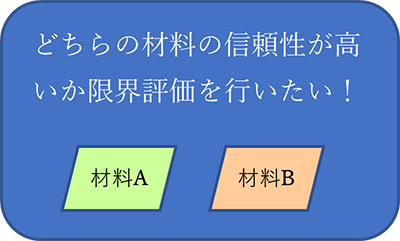
限界評価を行うには数か月の長時間がかかる
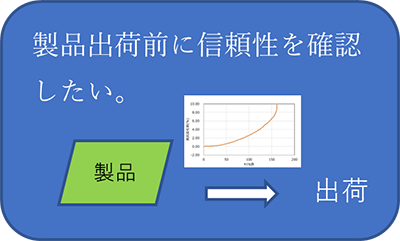
信頼性の確認に時間がかかり出荷に間に合わない
IST評価なら、従来の信頼性評価に比べて1/10~1/15の時間で信頼性の確認が可能
IST試験
IST:Interconnect Stress Test [試験規格:IPC-TM-650 2.6.26(A)]
配線パターンに印加した電流の発熱で配線板内部から加熱する方法
◆お客様のメリット
大幅な評価時間短縮!
- プリント配線板のVIA耐熱信頼性評価の時間短縮(90~95%削減)
- 新規材料開発・採用のスピードアップ
- 日常検査への長期信頼性評価の採用
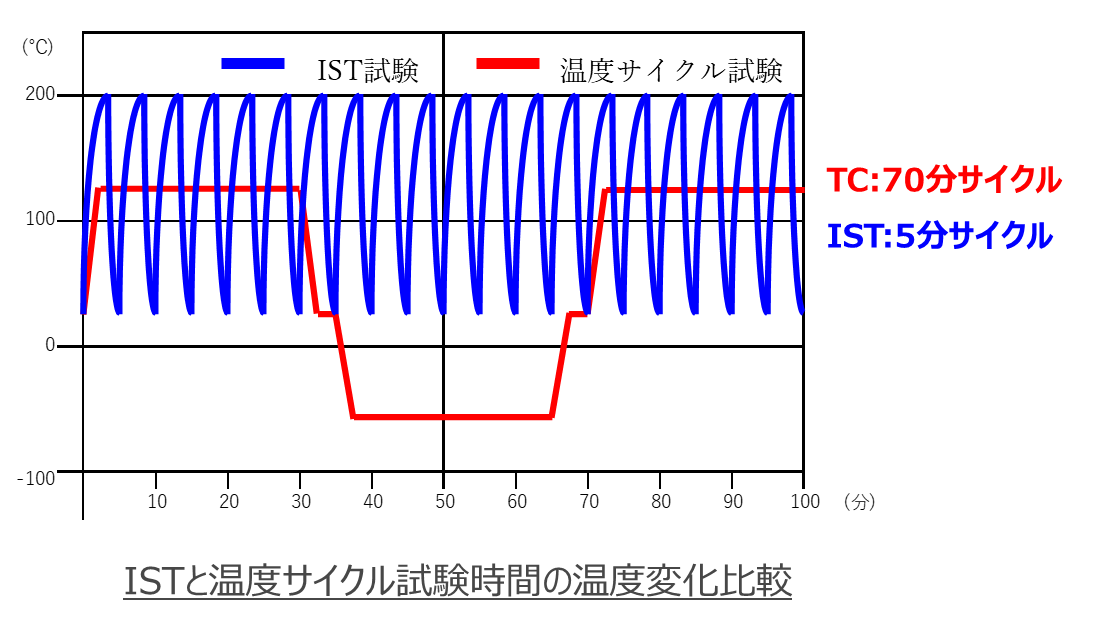
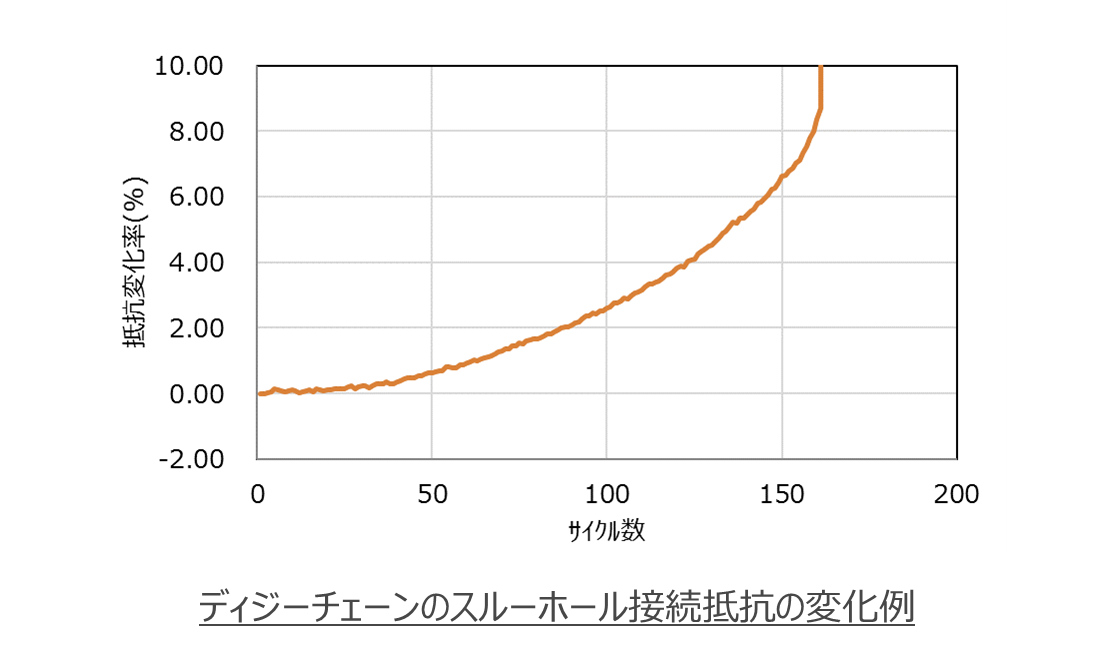
◆特徴・強み
- 材料Tg温度以上リフロー温度(260℃程度)までの温度サイクル評価が可能
- 評価基板パターン設計~基板製造~評価までワンストップ受託が可能
評価設備 | 評価時間 | 同時評価数 | 試験温度範囲 | 評価時間例 |
---|---|---|---|---|
温度サイクル試験機 | 70分/サイクル | 試験槽・サンプルサイズによる | -65~+150℃ | 50サイクル:約3日 1000サイクル:約2か月 |
IST試験機 | 5分/サイクル | Max8サンプル | 常温~+260℃ | 50サイクル:約5時間 1000サイクル:3~4日 |
IST試験機:IST-HC
(PWB interconnect solutions inc.)
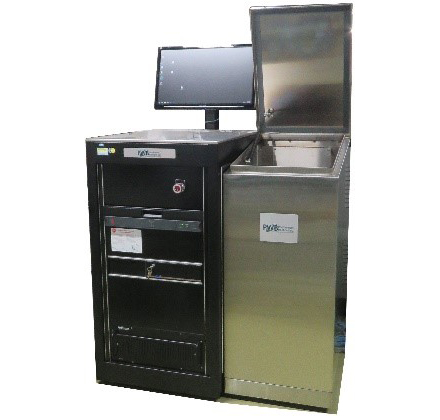
評価用基板
(25×120mm)
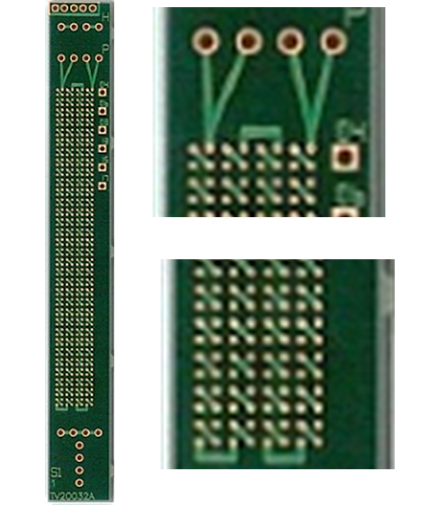
スルーホール断線クラック
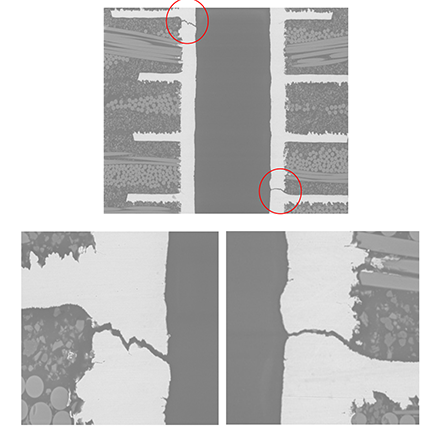
◆受託内容
【試験場所】協業先:NTTデバイスクロステクノロジ株式会社(日本国内で評価可能)
【試験対象物】
- 基板種類:多層・両面リジッド基板の他、薄板フレックス両面基板の評価も可能
- 基板材料:FR-4材、高Tg材、高速伝送材、ポリイミド材、LCP材
- 基板層構成・VIA種類:貫通スルーホール基板、張り合わせIVH基板、レーザVIAビルドアップ基板など基板種・VIA種を問わず評価可能
- 適用分野:5G/ミリ波帯機器、カーエレクトロニクス(車載)機器、航空/宇宙機器など向けの新規材料・高耐熱要求機器分野に最適
【受託内容】
- 評価基板の設計
- お客様で基板設計される場合の評価基板設計コンサル、評価条件・基板構造/仕様コンサル
- 評価基板製造コンサル(ご希望の基板メーカ様での製造に当たり、さまざまなコンサル・フォローをいたします)
- 基板メーカ紹介・取次ぎ(評価に最適な基板メーカ様のご紹介、基板製造取次ぎのご協力をいたします)
※基板製造はお客様からの直接発注でも、弊社経由の発注でも受託可能です。 - IST評価
- 評価後故障解析
- オプション評価:過熱によるデラミネーション(内層剥離)評価
【評価前処理】IST評価前に、部材・製品保管条件や実装条件に即した、サンプルへのさまざまな前処理が可能
- 実装熱履歴印加(IST装置によるプリコンディショニングとリフロー炉による実熱処理の選択が可能)
- 高温・低温放置処理
- ベーキング(乾燥)処理
- 温度サイクル処理
- 加湿処理
【故障解析】
- X線CT観察、サーモグラフィーによる断線個所検出
- 断面観察による断線個所観察(顕微鏡観察、SEM観察)
- 不具合原因究明、対策コンサル
プリント板のビア接続信頼性評価
◆ビア断線の原因
プリント板を構成する材料(銅と基材)には熱膨張係数に差があるため、周囲の温度変化により基板が伸縮し、ビアに歪みが発生・蓄積され、断線不具合(クラック)が発生します。
α1:ガラス転移温度以下の熱膨張率
α2:ガラス転移温度以上の熱膨張率
◆接続信頼性に影響する主な要因
主な要因 | |
---|---|
基板材料 | 基材の熱膨張率、ガラス転移温度 |
基板設計仕様 | 板厚、めっき厚、スルーホール径 |
◆従来のビア接続信頼性評価
周囲温度を変化することでサンプルの温度を上下させ、ビアに繰り返し歪みを加えることでビアの接続信頼性耐力を評価する評価方法。
例)温度サイクル試験
ISTを用いた評価の提案(1)
◆プリント板採用評価
現状品に対して新規材料や新規仕様の基板の信頼性を短期間で相対比較できます
- 設計上流での低コスト追及
①低コスト材料の選定
②銅めっき厚薄化による製造時間短縮 - 設計上流での製造品質確保
①デスミア条件の最適化(スルーホール内層接続不具合、レーザビア底断線不具合などの予防)
②高温時の断線(疑似接触不具合)の検出(不良流出の撲滅)
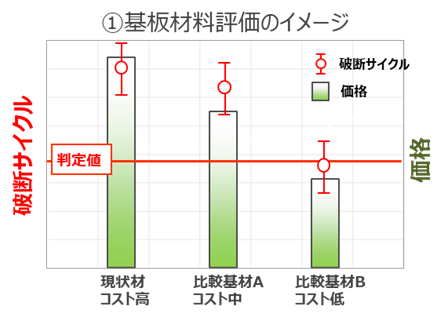
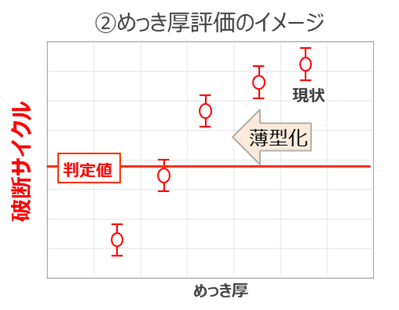
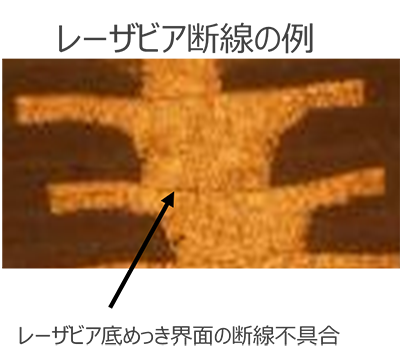
ISTを用いた評価の提案(2)
◆プリント板品質の定期検証
良品ロットを基準に量産基板の信頼性を日常的に定期評価できます
- 量産品の信頼性低下を検出(出荷前に不良流出を防止)
①めっき前洗浄異常による密着力低下を検出
②デスミア異常による密着力低下を検出
③レーザ加工異常によるビア径不良の検出
④スルーホールめっき異常の検出
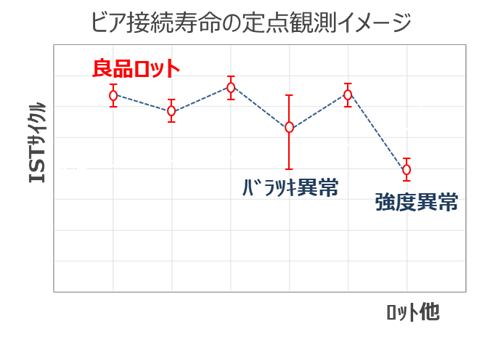